In the intricate world of engineering and automation, precision and control are paramount. Hydraulic actuators, often hidden from view, play a pivotal role in achieving these goals. In this comprehensive guide, we will unravel “what is hydraulic actuators”, exploring what they are, how they work, the various types, their applications, and much more. So, let's embark on a journey to understand the power behind precision and control.
Table of Contents
ToggleUnderstanding Hydraulic Actuators: what is it?
Hydraulic actuators are mechanical devices that convert fluid power, typically from hydraulic fluid pressure, into mechanical motion. They serve as vital components in various machines and systems, providing the force needed to perform a wide range of tasks.
The Mechanism Behind Hydraulic Actuators
Hydraulic actuators are fascinating devices that harness the power of fluid pressure to create controlled mechanical motion. To understand how they work, it's essential to delve into the intricacies of their mechanism. In this section, we'll explore the fundamental principles that drive hydraulic actuators and make them such valuable components in various industrial and engineering applications.
The Role of Hydraulic Fluid
At the heart of every hydraulic actuator lies hydraulic fluid, typically oil. This fluid serves as the medium for transmitting force from one part of the actuator to another. When pressure is applied to the hydraulic fluid, it becomes highly resistant to compression. This property is crucial because it allows the fluid to transmit force effectively.
The Cylinder: A Key Component
A common design in hydraulic actuators involves a cylinder with a piston inside it. The piston is a crucial component responsible for creating motion. When pressure is applied to one side of the piston, it moves in response, transferring force to the object it's connected to.
Pressure Difference
The key to the hydraulic actuator's mechanism lies in the pressure difference between the two sides of the piston. Here's how it works:
- Pressure Applied: Hydraulic fluid is pressurized and introduced into one side of the piston. This pressurized fluid exerts force on the piston, causing it to move.
- Fluid Transfer: As the piston moves, it pushes the hydraulic fluid on the opposite side back into the reservoir or another chamber, creating a pressure difference.
- Resultant Motion: The motion of the piston is transferred to the connected object or load, performing the desired work, whether it's lifting, pushing, or any other mechanical action.
Control Valves
Control valves play a pivotal role in the hydraulic actuator's mechanism. They regulate the flow of hydraulic fluid into and out of the actuator, enabling precise control over the actuator's movement. By adjusting the flow rate and direction of the hydraulic fluid, control valves determine the speed and direction of the actuator's motion.
Amplifying Force
One of the most remarkable aspects of hydraulic actuators is their ability to amplify force. Because hydraulic fluid is nearly incompressible and can transmit pressure evenly, a relatively small force applied to the piston can result in a much larger force at the output end. This property makes hydraulic actuators highly efficient and capable of handling heavy loads with ease.
Precision and Control
The hydraulic actuator's mechanism allows for precise and controlled motion. By regulating the pressure and flow of hydraulic fluid, engineers and operators can achieve accuracy down to fractions of a millimeter. This level of control is essential in applications where precision is paramount, such as in manufacturing, aerospace, and robotics.
The mechanism behind hydraulic actuators relies on the properties of hydraulic fluid, the movement of a piston, and the control valves that manage fluid flow.
Types of Hydraulic Actuators
Hydraulic actuators come in various types, each designed for specific applications and types of motion. Here are some common types of hydraulic actuators:
Hydraulic Cylinders:
Single-Acting Hydraulic Cylinder:
These cylinders have a single hydraulic port for fluid entry, and the motion is achieved by hydraulic pressure acting on one side of the piston. An external force or spring returns the piston to its original position when hydraulic pressure is released.
Double-Acting Hydraulic Cylinder:
Double-acting cylinders have hydraulic ports on both sides of the piston. Hydraulic pressure can be applied alternately to extend and retract the piston, allowing for bidirectional linear motion.
Hydraulic Motors:
Hydraulic Gear Motors:
These motors use a set of meshing gears to convert hydraulic pressure into rotary motion. They are known for their compact size and high-speed operation.
Hydraulic Vane Motors:
Vane motors use sliding vanes that are pushed by hydraulic pressure to create rotary motion. They are often used in low-speed, high-torque applications.
Hydraulic Piston Motors:
Piston motors use one or more pistons inside cylinders to generate rotary motion. They are known for their high efficiency and power output.
Hydraulic Rotary Actuators:
Rotary Vane Actuators:
These actuators convert hydraulic pressure into rotary motion using a vane mechanism. They are commonly used for applications like turning valves and dampers.
Rotary Piston Actuators:
Similar to hydraulic piston motors, rotary piston actuators use pistons to generate rotary motion. They are often used for high-torque applications, such as positioning heavy loads.
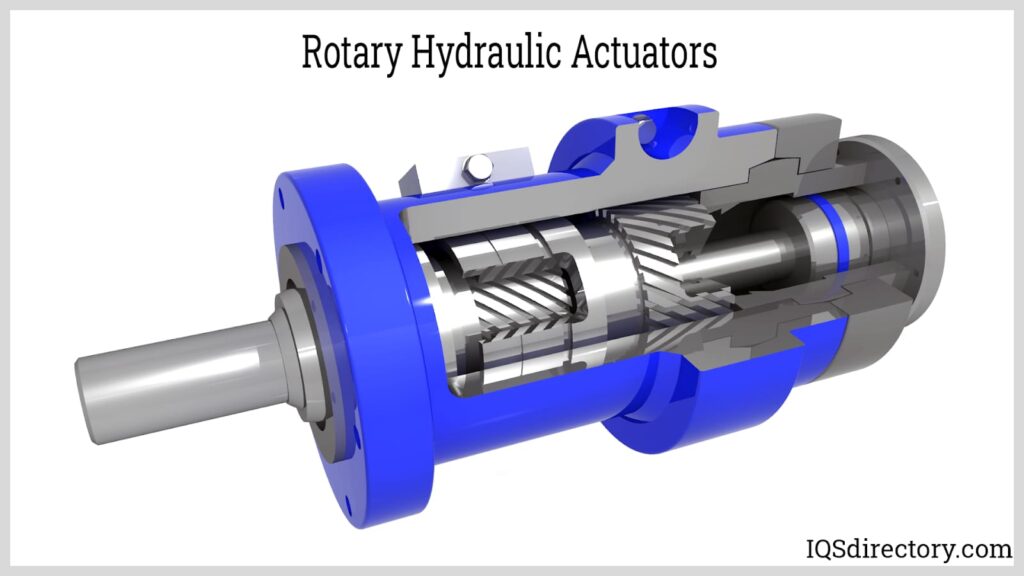
Image courtesy: IQSdirectory.com
Hydraulic Linear Actuators:
These actuators use a hydraulic piston to produce linear motion directly. They are used in applications where high force and precise linear movement are required.
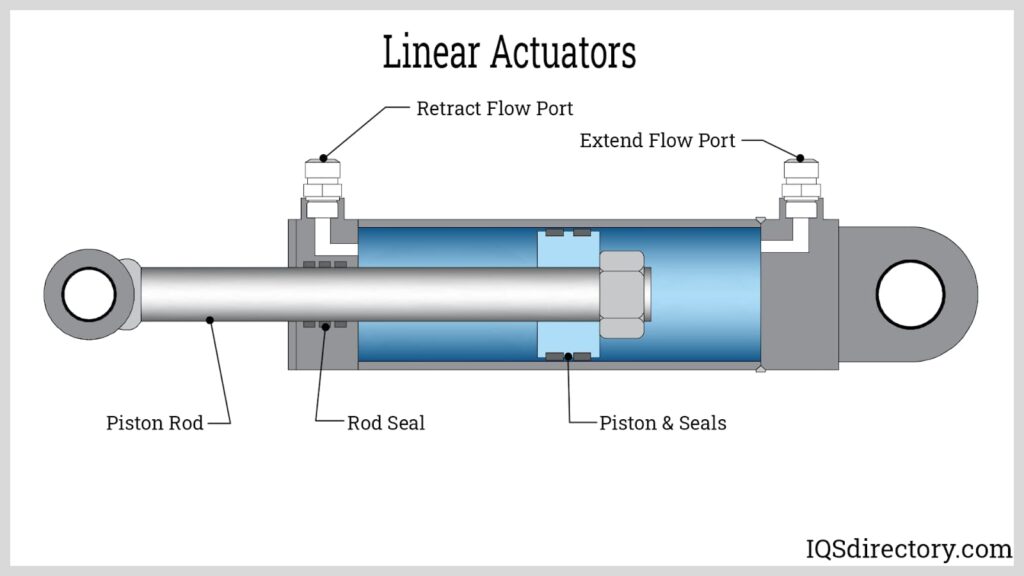
Image courtesy: IQSdirectory.com
Reference: https://www.hydrauliccylindermanufacturers.net/hydraulic-actuators/
Hydraulic Intensifiers:
These devices amplify the hydraulic pressure using a small piston to pressurize a larger piston. They are used in situations where a higher force or pressure is needed temporarily.
Hydraulic Accumulators:
Accumulators store hydraulic fluid under pressure, allowing it to be released when needed to provide an immediate burst of power. They are often used in emergency systems and for shock absorption.
Hydraulic Actuated Valves:
These actuators are designed to control the opening and closing of valves in hydraulic systems, enabling precise fluid flow control.
Hydraulic Servo Actuators:
These actuators combine hydraulic power with electronic control systems, offering precise and responsive motion control. They are often used in robotics and automation.
These various types of hydraulic actuators serve a wide range of applications across industries, providing the capability to control and move loads with precision, power, and versatility. The choice of actuator type depends on the specific requirements of the application, including the desired type of motion, force, and operational conditions.
Read More: https://plcdcscontrol.com/stepper-motor-introduction/
How Hydraulic Actuators Work
Hydraulic actuators work based on the principles of fluid dynamics and Pascal's law to convert hydraulic pressure into mechanical force or motion. Here's a step-by-step explanation of how hydraulic actuators work:
- Hydraulic Fluid: Hydraulic actuators operate using a specialized fluid, typically hydraulic oil. This fluid is chosen for its incompressible nature, which allows it to transmit force effectively.
- Reservoir: A hydraulic system includes a reservoir or tank that holds the hydraulic fluid. This is where the fluid is stored and returned to after it has been used in the system.
- Pump: The hydraulic system has a hydraulic pump that pressurizes the fluid by drawing it from the reservoir and forcing it into the system. The pump creates a flow of pressurized hydraulic fluid.
- Valves: The system incorporates various valves that control the flow of hydraulic fluid. Directional control valves determine the direction of fluid flow, while pressure relief valves protect the system from overpressure.
- Cylinder or Motor: The hydraulic actuator can be in the form of a hydraulic cylinder or a hydraulic motor, depending on the desired type of motion (linear or rotary).
- Hydraulic Cylinder: In the case of a hydraulic cylinder, the pressurized fluid is directed to one side of the cylinder, creating pressure against a piston. The piston is attached to a rod, and as the pressure builds, it pushes the rod outward, resulting in linear motion. This motion can be used for tasks like lifting, pushing, or pulling.
- Hydraulic Motor: A hydraulic motor uses the pressurized fluid to turn a rotor within the motor, generating rotary motion. This type of actuator is commonly used for applications such as rotating wheels, gears, or other mechanical components
- Load or Work: The hydraulic actuator's output (linear or rotary motion) is used to perform work or move loads. For example, in a hydraulic press, the linear motion of the hydraulic cylinder is used to compress or shape materials.
- Return Flow: After the hydraulic fluid has performed its work, it returns to the reservoir through a return path. In the case of a hydraulic cylinder, the fluid on the opposite side of the piston is allowed to flow back to the reservoir. In a hydraulic motor, the fluid exits the motor and returns to the reservoir.
- Control and Feedback: Control of the hydraulic actuator's movement and position is achieved by adjusting the flow of hydraulic fluid through the system using control valves. Feedback devices such as position sensors or pressure sensors may be used to monitor and control the actuator's operation accurately.
- Safety and Maintenance: Safety features, including pressure relief valves and filters, are incorporated into the hydraulic system to protect it from damage and ensure safe operation. Regular maintenance is essential to keep the hydraulic system in good working condition.
In summary, hydraulic actuators work by utilizing the pressure of hydraulic fluid to create mechanical force or motion.
Applications of Hydraulic Actuators
Hydraulic actuators find applications in a wide range of industries and systems due to their ability to provide powerful and precise movement. Here are some key applications of hydraulic actuators:
- Industrial Machinery: Hydraulic actuators are used in various industrial machines, including presses, shears, and metal-forming equipment, to provide the force needed for bending, cutting, and shaping metal and other materials.
- Construction Equipment: Hydraulic actuators power heavy machinery like excavators, bulldozers, and cranes, enabling them to lift and move heavy loads, dig trenches, and perform other essential construction tasks.
- Aerospace: Hydraulic actuators are used in aircraft for functions like extending and retracting landing gear, controlling flight surfaces (flaps, ailerons, rudders), and actuating cargo doors.
- Automotive Industry: In vehicles, hydraulic actuators are employed in braking systems, power steering systems, and automatic transmissions. They provide precise control and responsiveness for safe and efficient driving.
- Agricultural Machinery: Hydraulic actuators are used in tractors, combines, and other agricultural equipment to power various functions, such as lifting and lowering attachments, steering, and controlling implements like plows and seeders.
- Marine Industry: Hydraulic actuators are utilized in boats and ships for functions like steering systems, anchor deployment, and controlling hatches and doors.
- Material Handling: They are used in material handling equipment such as forklifts, conveyors, and palletizers to lift, move, and position heavy loads efficiently.
- Oil and Gas Industry: Hydraulic actuators are essential in the oil and gas sector for controlling drilling equipment, valves, and other machinery used in drilling, extraction, and processing operations.
- Manufacturing Automation: Hydraulic actuators play a crucial role in automated manufacturing processes, including robotic assembly lines and CNC machinery, where they provide precise control and positioning.
- Mining Equipment: Hydraulic actuators are used in mining machinery for functions such as rock drilling, ore transportation, and controlling heavy equipment like bulldozers and loaders.
- Civil Engineering: They are employed in civil engineering applications like bridge and dam construction, where large structures and heavy materials need to be moved and positioned accurately.
- Environmental and Waste Management: Hydraulic actuators are used in waste compactors, recycling equipment, and waste handling systems to compress and process waste materials efficiently.
- Medical Devices: In the medical field, hydraulic actuators are used in various equipment, such as patient lifts, surgical tables, and diagnostic devices, to provide precise movement and positioning.
- Defense and Military: Hydraulic actuators are used in military vehicles, aircraft, and equipment for various applications, including weapon systems, landing gear, and vehicle mobility.
- Entertainment Industry: Hydraulic actuators are employed in stage and entertainment equipment, such as hydraulic lifts, platforms, and special effects devices used in theaters, concerts, and theme parks.
- Environmental Control Systems: They are used in environmental control systems for tasks like adjusting the position of air dampers and valves in heating, ventilation, and air conditioning (HVAC) systems.
- Offshore Drilling: In offshore drilling platforms, hydraulic actuators control various equipment, including the positioning of drilling rigs, pipe handling systems, and wellhead control.
- Railway Systems: Hydraulic actuators are used in railway applications for functions such as controlling brakes, doors, and switches.
These are just some of the many applications of hydraulic actuators across different industries and sectors, highlighting their versatility and importance in enabling precise and powerful mechanical operations.
Advantages of Hydraulic Actuators
Power and Precision
Hydraulic actuators offer a unique combination of power and precision. Understand why they excel in tasks that demand both force and accuracy.
Reliability and Safety
Reliability is a hallmark of hydraulic systems, and safety is paramount. Explore how hydraulic actuators provide dependable performance in critical applications.
Maintenance and Troubleshooting of Hydraulic Actuator
Maintenance and troubleshooting are critical aspects of ensuring the reliable and efficient operation of hydraulic actuators and the overall hydraulic system. Proper maintenance helps prevent costly breakdowns and downtime, while effective troubleshooting allows for the quick identification and resolution of issues. Here are some guidelines for maintenance and troubleshooting of hydraulic actuators:
Maintenance:
- Regular Inspection: Perform routine visual inspections of the hydraulic actuator, checking for signs of leaks, corrosion, loose fittings, or damaged components. Inspect hoses, seals, and connections for wear and tear.
- Fluid Inspection: Monitor the condition of the hydraulic fluid. Check fluid levels, cleanliness, and temperature regularly. Contaminated or degraded fluid can lead to actuator problems.
- Change Hydraulic Fluid: Follow the manufacturer's recommendations for changing hydraulic fluid. Contaminated or degraded fluid should be replaced promptly to maintain system performance.
- Filter Maintenance: Keep hydraulic filters clean or replace them as recommended by the manufacturer. Clogged filters can restrict fluid flow and lead to actuator issues.
- Seal Inspection: Inspect seals and gaskets for signs of wear, damage, or leakage. Replace seals that show signs of deterioration.
- Lubrication: Lubricate moving parts, such as bearings and linkages, as specified by the manufacturer to prevent friction-related problems.
- Tighten Bolts and Fittings: Regularly check and tighten bolts, fittings, and connections to prevent leaks or loosening over time.
- Pressure Relief: Ensure that pressure relief valves are functioning correctly to prevent overloading the actuator.
- Keep External Surfaces Clean: Keep the exterior of the actuator clean to prevent dirt and debris from entering the system.
Troubleshooting:
- Identify Symptoms: When a problem arises, start by identifying the specific symptoms. Is the actuator not moving, moving too slowly, or making unusual noises?
- Check Fluid Levels: Verify that there is an adequate supply of hydraulic fluid in the system. Low fluid levels can lead to inefficient operation.
- Check for Leaks: Inspect the system for hydraulic fluid leaks. Leaks can occur in hoses, fittings, seals, or the actuator itself. Address any leaks promptly.
- Check Pressure: Use pressure gauges to measure system pressure at various points. Low pressure can indicate issues with the pump, while high pressure can indicate a blockage or valve problem.
- Check Control Valves: Verify that control valves are functioning correctly and that they are receiving the appropriate signals from the control system.
- Check for Air in the System: Air trapped in the hydraulic system can cause sponginess and reduced performance. Bleed the system to remove air bubbles.
- Inspect Electrical Connections: If the actuator is electronically controlled, check electrical connections for loose or damaged wires.
- Review Maintenance Records: Consult maintenance records to see when the actuator and hydraulic system were last serviced. It can provide valuable insights into potential issues.
- Consult Manuals and Documentation: Refer to the manufacturer's manuals and documentation for troubleshooting guidelines specific to your actuator model.
- Seek Professional Help: If you are unable to identify or resolve the issue, it's advisable to seek assistance from a qualified hydraulic technician or engineer who can diagnose and repair the problem.
Regular maintenance and effective troubleshooting practices are essential for maximizing the lifespan and efficiency of hydraulic actuators. Addressing issues promptly and following a proactive maintenance schedule can prevent costly breakdowns and keep hydraulic systems operating smoothly.
Hydraulic Actuators vs. Electric Actuators
A Comparison
Hydraulic actuators and electric actuators are two distinct types of devices used for controlling and manipulating mechanical systems. They operate on different principles and offer various advantages and disadvantages. Let's compare hydraulic actuators and electric actuators in terms of their key characteristics:
Hydraulic Actuators:
- Power Source: Hydraulic actuators are powered by pressurized hydraulic fluid (usually oil). They rely on hydraulic pumps to generate this pressure.
- Force Output: Hydraulic actuators are known for their high force output, making them suitable for applications requiring substantial power, such as heavy machinery and construction equipment.
- Precision and Control: They provide excellent precision and control over movement and force, which is crucial in applications where accuracy is essential.
- Speed: Hydraulic actuators can operate at variable speeds, but their response time may be slower compared to electric actuators.
- Energy Efficiency: They can be energy-efficient when designed with the right hydraulic components, but the overall energy efficiency depends on the system's design and maintenance.
- Maintenance: Hydraulic systems require regular maintenance to ensure the hydraulic fluid remains clean and free from contamination. This maintenance can be more involved than electric systems.
- Environmental Considerations: Hydraulic systems may leak hydraulic fluid, which can be harmful to the environment. Proper containment and disposal procedures are essential.
- Applications: Hydraulic actuators are commonly used in heavy machinery, automotive braking systems, aircraft landing gear, and industrial applications.
Electric Actuators:
- Power Source: Electric actuators are powered by electricity and do not require hydraulic fluid. They are more straightforward in terms of power source.
- Force Output: Electric actuators typically have lower force outputs compared to hydraulic actuators. They are more suited for applications that require precision and control over raw power.
- Precision and Control: Electric actuators excel in providing precise control and can offer accurate positioning, making them suitable for tasks like robotics and automation.
- Speed: Electric actuators are known for their fast response times and can achieve rapid motion and positioning.
- Energy Efficiency: They are generally more energy-efficient than hydraulic systems because they only consume electricity when in use. There is no continuous power loss due to hydraulic pump operation.
- Maintenance: Electric actuators require less maintenance than hydraulic systems since there is no hydraulic fluid to manage. However, electrical components may require occasional maintenance.
- Environmental Considerations: Electric actuators are cleaner in terms of environmental impact since they don't involve hydraulic fluid and the associated risks of leakage.
- Applications: Electric actuators are widely used in precision applications such as robotics, CNC machinery, medical devices, and home automation systems.
The Future of Hydraulic Actuators
Technological Advancements
What we can expect in the field of hydraulic actuators:
- Electro-Hydraulic Actuators: The development of advanced electro-hydraulic actuators will combine the benefits of hydraulic power with electric control. These actuators will use highly efficient electric servos to control hydraulic systems, providing precise and rapid movement while minimizing energy consumption.
- Smart Hydraulic Systems: Future hydraulic actuators will be equipped with smart sensors and monitoring systems that continuously collect data on pressure, temperature, fluid quality, and component wear. Machine learning algorithms will use this data for predictive maintenance, optimizing performance, and minimizing downtime.
- Energy-Efficient Pumps: Hydraulic pumps, a crucial component of hydraulic systems, will see advancements in design and efficiency. Variable displacement pumps with intelligent control will adapt to the actual load requirements, reducing energy consumption and heat generation.
- Nanotechnology-Enhanced Components: Nanotechnology will be applied to hydraulic actuators to develop nano-coatings and materials that reduce friction and improve efficiency. These nanomaterials will also enhance the wear resistance of critical components, extending the lifespan of hydraulic systems.
- Digital Hydraulics: Digital hydraulic systems will become more prevalent, utilizing digital valves and control algorithms to achieve precise control, faster response times, and increased energy efficiency. Digital hydraulics can vary the flow rates and pressures digitally, optimizing performance for specific tasks.
- Energy Recovery Systems: Hydraulic actuators will incorporate energy recovery systems that capture and store excess energy during deceleration or load lowering. This stored energy can be reused to power the system during acceleration or heavy load cycles, improving overall energy efficiency.
- Advanced Materials: Hydraulic components will benefit from advanced materials like carbon fiber-reinforced composites and lightweight alloys. These materials will reduce the weight of hydraulic actuators, making them more suitable for aerospace and automotive applications.
- Additive Manufacturing: 3D printing and additive manufacturing techniques will enable the production of complex hydraulic components with optimized geometries. This will lead to custom-designed actuators that are lighter, more efficient, and cost-effective to produce.
- Remote Monitoring and Control: Hydraulic systems will feature remote monitoring and control capabilities, allowing operators to adjust settings, diagnose issues, and perform maintenance tasks from a distance. This will enhance efficiency and reduce the need for on-site maintenance.
- Environmentally Friendly Hydraulic Fluids: The development of biodegradable and eco-friendly hydraulic fluids will become more widespread to address environmental concerns associated with hydraulic systems. These fluids will offer comparable performance while being less harmful to the environment.
- Precision Positioning: Hydraulic actuators used in precision manufacturing and robotics will incorporate advanced position feedback mechanisms, such as laser interferometry or magnetic encoders, to achieve sub-micron-level accuracy in positioning.
- High-Pressure Hydraulics: Advancements in materials and sealing technologies will enable hydraulic systems to operate at even higher pressures, expanding their use in heavy-duty applications where extreme force is required.
These specific advancements in hydraulic actuators represent a glimpse into the future of this technology, where increased efficiency, precision, and sustainability will drive their adoption across a broader range of industries and applications.
Choosing the Right Hydraulic Actuator
Factors to Consider
Choosing the right hydraulic actuator is essential to ensure the successful performance of your hydraulic system. Several factors must be considered when making this decision:
Application Requirements:
Determine the specific requirements of your application, including the required force or torque, speed, and precision of movement. Different hydraulic actuators are better suited for different tasks, so matching the actuator to the application is crucial.
Load Capacity:
Calculate the load or weight that the actuator needs to move or control. Ensure that the selected actuator has sufficient force or torque capacity to handle the load without overloading.
Motion Type:
Decide whether your application requires linear or rotary motion. Hydraulic cylinders are used for linear motion, while hydraulic motors provide rotary motion. Select the type of actuator that aligns with your application's needs.
Speed Requirements:
Consider the desired speed of operation. Some hydraulic actuators are better suited for high-speed applications, while others are designed for slow, precise movements. Ensure that the actuator's speed capabilities match your requirements.
Space Constraints:
Assess the available space in your system. Hydraulic actuators come in various sizes and configurations, so choose one that fits within the space constraints of your application.
Environmental Conditions:
Evaluate the environmental conditions in which the actuator will operate. Factors such as temperature extremes, exposure to corrosive substances, or high-pressure environments can affect actuator performance. Select an actuator that can withstand these conditions.
Energy Efficiency:
Consider energy efficiency requirements. Some hydraulic systems are designed with energy-saving features, which can be important for long-term operational costs and environmental sustainability.
Control System Compatibility:
Ensure that the chosen hydraulic actuator is compatible with your control system. The actuator should work seamlessly with your control components, sensors, and software.
Maintenance and Serviceability:
Assess the ease of maintenance and availability of replacement parts. Opt for an actuator that allows for straightforward maintenance and easy access to critical components.
Cost and Budget:
Determine your budget constraints. Hydraulic actuators vary in cost based on their capabilities and features. Balance your requirements with your budget to find the most cost-effective solution.
Safety Considerations:
Consider safety features, especially in applications involving human-machine interaction. Ensure that the actuator has safety mechanisms to prevent accidents or injury.
Future Expansion and Upgrades:
Think about future needs and the potential for system expansion or upgrades. Choosing a versatile actuator that can adapt to changing requirements can save time and resources in the long run.
By carefully evaluating these factors and consulting with experts in hydraulic systems, you can make an informed decision when choosing the right hydraulic actuator for your specific application.
FAQs About Hydraulic Actuators
Q. What is the primary function of a hydraulic actuator?
Hydraulic actuators convert hydraulic fluid pressure into mechanical motion, enabling them to perform tasks such as lifting, pushing, or rotating.
Q. What industries rely heavily on hydraulic actuators?
Industries such as manufacturing, construction, aerospace, automotive, and more rely on hydraulic actuators for precise and powerful motion control.
Q. How do hydraulic actuators compare to electric actuators in terms of precision?
Hydraulic actuators excel in tasks that require a combination of power and precision, making them ideal for applications where accuracy is crucial.
Q. What maintenance tasks are essential for hydraulic actuators?
Regular maintenance includes addressing fluid leaks, replacing seals, and ensuring proper lubrication to keep hydraulic actuators in optimal condition.
Q. Are hydraulic systems safe to use in critical applications?
Yes, hydraulic systems are known for their reliability and safety. They are commonly used in critical applications that demand dependable performance.
Q. What are the latest trends in hydraulic actuator technology?
Technological advancements in hydraulic actuator technology include improved materials, precision control systems, and enhanced efficiency.
Watch our video on hydraulic actuators :
Conclusion
As we conclude our journey through the world of hydraulic actuators, one thing becomes clear: these unassuming devices are the unsung heroes of precision and control. From heavy machinery to aerospace exploration, hydraulic actuators empower industries with the force and accuracy needed to shape our modern world. Understanding their mechanisms, types, applications, and advantages is a valuable asset for anyone venturing into the realm of engineering and automation.