Did you know that the heart of modern industrial automation lies in a technology called Remote IO? It refers to a configuration where the IO devices are physically located at a distance from the central PLC unit. This setup is commonly used in industrial automation and control systems to extend the reach of the PLC's control. These distributed IOs are designed to interface with sensors, actuators, and other control devices located in remote or harsh environments.
In this blog post, we'll embark on a journey through the world of Remote IO, exploring its definition, benefits, components, applications, and the crucial role it plays in enhancing the functionality of PLCs.
Later on this blog we will discuss the feature of Siemens ET200 distributed IO module.
Table of Contents
ToggleUnderstanding Remote IO
The primary purpose of Remote IO is to facilitate communication between the centralized PLCs. Without Remote IO, PLCs would be limited in their ability to interface with these devices. The significance of Remote IO becomes apparent when you consider its role in extending the reach of PLCs. It allows PLCs to access data from sensors and provide control commands to actuators that are geographically dispersed or located in areas with adverse conditions. This extension of reach is crucial for industries where precision control and real-time data acquisition are paramount.
Imagine a manufacturing plant with sensors monitoring temperature, pressure, and flow rates at various points in the production process. These sensors may be scattered across the facility, sometimes in harsh or hazardous locations. Remote IO modules act as the eyes and ears of the PLC, collecting data from these sensors and transmitting it to the central controller. Simultaneously, the PLC uses Remote IO to send commands to actuators, ensuring that the production process stays on track.
Benefits of using remote IO for PLCs
Flexibility: Remote IO allows for the placement of sensors and actuators in remote or hazardous locations while keeping the central control logic in a more controlled environment.
Scalability: Systems can be easily expanded by adding additional remote IO modules as needed, but no major changes required to the central PLC.
Reduced Wiring Costs: Remote IO systems can significantly reduce the amount of wiring as compared to a traditional centralized PLC setup.
Improved Maintenance: Troubleshooting and maintenance become more accessible as field devices are located in centralized cabinets, making them easier to access.
Components of a Remote IO System
Central PLC Unit & remote IO: The central PLC unit is the brain of the control system. It contains the CPU (Central Processing Unit), memory, and programming logic. The PLC is responsible for processing control algorithms and making decisions based on inputs received from remote IO modules.
Remote IO Modules: These are the devices placed in remote locations to interface with field devices. Remote IO modules come in various types, including IO modules. Input modules are used to acquire signals from sensors and other devices, while output modules are responsible for controlling actuators such as motors and valves.
Communication Network: A communication network connects the central PLC unit to the remote IO modules. Different communication protocols may be used depending on the system's requirements. It can be Ethernet, Profibus, Modbus, DeviceNet, or others. The choice of protocol depends on factors like distance, data speed, and environmental conditions.
Wiring and Cabling: Proper wiring and cabling are crucial for transmitting signals between the central PLC and remote IO modules. Shielded cables are often used to minimize electrical interference and ensure reliable data transmission.
Remote IO Communication Protocols
In PLC remote IO systems, several communication protocols are commonly used to facilitate data exchange between the central PLC and remote IO modules. The choice of communication protocol depends on factors such as the specific PLC manufacturer, the type of IO system, and the application requirements. Here are some of the common communication protocols used in PLC remote IO systems:
Profibus:
Profibus (Process Field Bus) is a widely used communication protocol in industrial automation. It supports both peer-to-peer and master-slave communication.
Profibus DP (Decentralized Peripherals) is often used in remote IO applications. It allow the central PLC to communicate with remote IO devices over a high-speed network.
Profibus PA (Process Automation) is used for process automation applications, including communication with field instruments.
Modbus is a popular and simple communication protocol used in many PLC systems, including remote IO.
Modbus-RTU (Remote Terminal Unit) and Modbus TCP/IP are common variants used for serial and Ethernet-based communication, respectively.
It's often used for connecting PLCs to various devices, including remote IO modules, sensors, and actuators.
DeviceNet:
DeviceNet is a communication protocol primarily used for connecting industrial devices, including remote IO modules, sensors, and motor drives. It's based on the CAN (Controller Area Network) technology and is known for its simplicity and robustness.
EtherNet/IP:
EtherNet/IP is an Ethernet-based communication protocol that is increasingly used in industrial automation, including remote IO applications. It allows for high-speed data exchange and is compatible with standard Ethernet hardware.
Profinet:
Profinet is an Ethernet-based communication protocol developed by Siemens. It's commonly used with Siemens PLCs and remote IO systems. Profinet IO is often used for real-time communication with remote IO modules and other field devices.
The choice of communication protocol will depend on the specific requirements of the automation system, the PLC manufacturer's compatibility, and the existing infrastructure. It's essential to select the protocol that best suits your application and ensures reliable communication between the central PLC and remote IO modules.
Siemens ET 200 SP series
The ET 200 is a series of modular input/output (IO) systems produced by Siemens for use in industrial automation and control applications. These modules are designed to work with Siemens' SIMATIC S7 programmable logic controllers (PLCs) and are commonly used in a wide range of industries.
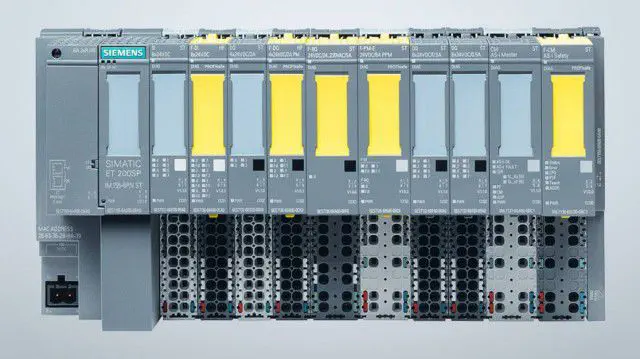
Image courtesy: www.siemens.com
The SIMATIC ET 200SP is a versatile and scalable distributed IO system offering a broad range of products while maintaining an efficient footprint. Designed for installation within control cabinets, it boasts an IP20 degree of protection. Notably, its redesigned layout and push-in terminals simplify cable wiring and disconnection processes.
In contrast, the SIMATIC ET 200pro is a rugged and high-performance modular distributed IO system boasting an impressive IP65/67 degree of protection. It finds its home outside control cabinets, directly at the machine. Thanks to its extensive array of modules, it excels in scenarios demanding fine-modular setups with diverse functionalities, even in challenging environmental conditions. It is particularly well-suited for applications involving electric monorail systems, automated guided vehicles, building management, and warehouse logistics, often with wireless connectivity.
Meanwhile, the SIMATIC ET 200AL stands out with its robust design and a high IP65/67 degree of protection. Its compact form factor, minimal space requirements, and lightweight construction make it ideal for distributed control electronics in confined spaces. This makes ET 200AL modules exceptionally resilient and an excellent choice for applications involving motion, even under continuous forces of up to 5 g and a maximum of 10 g.
Feature of Siemens ET 200 SP series hardware

Image courtesy: www.siemens.com
The specific technical details may vary depending on the model and version of the ET 200 module, here are some common technical specifications and features:
Modularity: The ET 200 series is modular, allowing users to customize their I/O systems to meet the specific requirements of their automation projects. Modules can be added or removed as needed.
Communication Protocols: ET 200 modules are compatible with various communication protocols, including PROFINET, PROFIBUS, and EhterNet IP. It also allow for flexible integration into different industrial networks as it comes with MultiFieldbus interface Module.
Input/Output Types: It support both digital and analog input and output types, such as DI, DO, AI, AO and special function modules. i.e. motor control and positioning.
Isolation: It provide electrical isolation between the field-side and the PLC-side of the system. This isolation helps protect the PLC from voltage spikes and noise generated in industrial environments.
Diagnostics: It often come equipped with diagnostics capabilities, allowing for the monitoring of module health and status remotely. This helps in troubleshooting and preventive maintenance.
Hot-Swapping: Some ET-200 modules support hot-swapping, which means you can replace or add modules without shutting down the entire system. This feature reduces downtime during maintenance or expansion.
Mounting Options: It can be mounted on a standard DIN rail or attached to a panel, making them easy to install in control cabinets.
Configuration: Configuration and parameterization of ET 200 modules are typically done through Siemens' TIA (Totally Integrated Automation) Portal software, which allows for easy setup and programming.
Watch our video on remote IO
Conclusion
Finally, In summary, remote IO is used in PLC systems to extend the reach of the controller and interface with field devices located at a distance or in challenging environments. It also offers benefits such as cost savings, flexibility, scalability, and improved reliability, making it a valuable component in industrial automation and control systems.
Happy Learning ..