Automation, at its core, as elements of industrial automation, involves the utilization of advanced control systems and technology to mechanize various tasks and processes within an industry, effectively reducing the need for human intervention. This transformative approach to manufacturing encompasses a broad spectrum of technologies, including robotics, sensors, and programmable logic controllers (PLCs). These technologies work in tandem to orchestrate and optimize production processes, ultimately enhancing efficiency, precision, and overall operational performance.
Table of Contents
ToggleDefinition of Industrial Automation
Industrial automation is defined by the integration of intelligent systems and technologies into industrial settings, enabling the automation of tasks that were traditionally carried out by human operators. This includes the use of sensors to gather data, programmable logic controllers to make decisions based on that data, and various actuators to execute physical processes. The overarching goal is to streamline manufacturing processes, reduce manual labor, and achieve a level of consistency and reliability that may be unattainable through manual means alone.
Importance of Industrial Automation in Manufacturing
The significance of industrial automation in manufacturing cannot be overstated. One of its key benefits lies in the substantial increase in efficiency it brings to production processes. By minimizing human involvement in routine and repetitive tasks, automation allows for continuous and optimized operation, leading to higher production rates and shorter cycle times. Furthermore, industrial automation enhances precision and accuracy, ensuring consistent product quality. This not only meets stringent industry standards but also contributes to a reduction in overall production costs through decreased waste and optimized resource utilization. Beyond economic advantages, automation improves workplace safety by assigning hazardous tasks to machines, allowing human operators to focus on complex, high-level responsibilities.
In a dynamic market, the adaptability and flexibility provided by industrial automation are crucial, enabling manufacturers to easily reconfigure processes and respond rapidly to changing demands. As a result, companies that embrace industrial automation gain a competitive edge, not only by improving operational efficiency but also by fostering innovation and agility in the face of evolving industry landscapes.
Basic Elements of Industrial Automation
In the intricate tapestry of industrial automation, the second act unfolds with an exploration of its fundamental components, focusing on the captivating duo of Sensors and Actuators.
Sensors and Actuators
Types of Sensors
- Proximity Sensors: These silent guardians of the manufacturing realm detect the nuanced dance of nearby objects, enhancing the symphony of precision within industrial processes.
- Pressure Sensors: Echoing the heartbeat of machinery, these sensors measure the pulse of forces at play, ensuring that processes unfold in perfect rhythm.
- Temperature Sensors: Functioning as storytellers of thermal tales, these sensors weave narratives of the manufacturing environment, offering insights into the dynamic temperature landscape.
Types of Actuators
- Motors: Emerging as the prolific poets of kinetic energy, motors infuse life into machinery with their rhythmic revolutions, driving the graceful choreography of manufacturing processes.
- Valves: As choreographers of fluidic movements, valves direct the elegant flow of liquids and gases, orchestrating a seamless performance in the industrial ballet.
- Pneumatic Actuators: Ethereal spirits of pressurized air, these actuators engage in a delicate dance, translating invisible forces into tangible actions, harmonizing with the overall machinery composition.
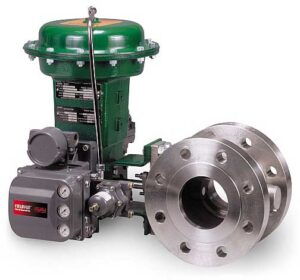
www.wermac.org
In this exploration of the basic elements of industrial automation, Sensors and Actuators emerge as the elemental artisans, each playing a unique role in the grand orchestration of efficiency and precision within the manufacturing realm.
Programmable Logic Controllers (PLCs)
As an elements of industrial automation we unravel the intricacies of Programmable Logic Controllers (PLCs), the master conductors orchestrating precision in modern manufacturing.

Image courtesy: www.siemens.com
Functions of PLCs
Delve into the core functionalities of PLCs, exploring their pivotal role in automating diverse manufacturing processes. From logic operations to sequence control, discover how PLCs serve as the brain of industrial automation.
Programming Languages for PLCs
- Ladder Logic: Ladder Logic acts as a bridge between traditional electrical relay systems and the digital realm of PLCs. It efficiently translates complex relay logic into a format compatible with PLC programming. This transformation allows for the seamless integration of advanced automation strategies without sacrificing the clarity of traditional relay-based control.
- Function Block Diagram (FBD): It is a visual representation of control logic using graphical blocks to represent functions and their interconnections. It provides a systematic approach to programming industrial processes, making it a key player in Programmable Logic Controllers (PLCs) and other automation systems.
- Structured Text: Structured Text is a high-level programming language designed for the specification of programmable logic controllers. Unlike ladder logic or function block diagrams, ST resembles traditional programming languages, making it accessible to those familiar with software development.
Explore more regarding Siemens PLC
HMI as elements of industrial automation
The primary function of HMI (Human-Machine Interface) is to provide real-time monitoring and control of industrial processes. Operators can visualize critical data, monitor machine statuses, and intervene promptly in case of anomalies, ensuring seamless and efficient operations as an elements of industrial automation.
Role of HMI in Industrial Automation
HMI serves as the bridge that transforms intricate machine data into a comprehensible format for human operators. Through intuitive graphical interfaces, touchscreens, and controls, it facilitates seamless interaction, empowering operators to monitor, control, and optimize industrial processes.
Design Principles for Effective HMIs
Information should be organized based on its importance and relevance. Prioritizing information hierarchies ensures that operators can quickly access critical data without being overwhelmed by less pertinent details. Clear hierarchies contribute to a more efficient decision-making process.
Communication Systems
Embark on a comprehensive exploration of Communication Systems in elements of industrial automation, unraveling the intricate networks that facilitate seamless connectivity in the realm of industrial automation.
Fieldbus Systems
- Profibus: Profibus, short for Process Field Bus, stands out as a leading communication protocol in the realm of industrial automation. Developed to address the communication challenges within fieldbus systems, Profibus has become a cornerstone in connecting and orchestrating diverse devices within automated processes.
- DeviceNet: DeviceNet, a protocol developed by Allen-Bradley (now a part of Rockwell Automation), revolves around the principle of providing a standardized network for connecting industrial devices.
- Modbus: Modbus, a protocol with humble beginnings developed by Modicon (now Schneider Electric), was designed to establish communication between programmable logic controllers (PLCs) and various industrial electronic devices. Over the years, its simplicity and versatility have contributed to its widespread adoption in diverse industrial applications.
Industrial Ethernet as elements of industrial automation
- EtherNet/IP: EtherNet/IP, an extension of the widely adopted Ethernet standard, brings the power of this ubiquitous network technology to the realm of industrial automation. Developed by the Open DeviceNet Vendor Association (ODVA), EtherNet/IP combines the benefits of standard Ethernet with an open, scalable platform tailored for industrial applications.
- PROFINET: PROFINET, short for Process Field Network, represents a standardized Industrial Ethernet solution designed to facilitate seamless communication and integration across various devices within an industrial network. Developed and maintained by PROFIBUS & PROFINET International (PI), PROFINET combines the ubiquity of Ethernet with industrial automation specificity.
- Modbus TCP/IP: Modbus TCP/IP, an extension of the Modbus protocol, represents a shift towards Internet Protocol (IP)-based communication in industrial settings. It builds upon the simplicity and versatility of the original Modbus protocol while harnessing the ubiquity and familiarity of TCP/IP, the backbone of the modern internet.
Advanced elements of industrial automation
Embark on a journey through the intricate realm of Advanced elements of industrial automation, unraveling the complexities and applications that define modern industrial automation.
Industrial Robots as elements of industrial automation
Types of Industrial Robots
- Articulated Robots: Articulated robots belong to the family of robotic arms characterized by rotary joints. Mimicking the flexibility of the human arm, these robots consist of multiple interconnected segments, each controlled by rotary joints. This design allows for a wide range of motion and intricate tasks.
- Cartesian Robots: Cartesian robots derive their name from the Cartesian coordinate system, emphasizing their linear and orthogonal movement along the X, Y, and Z axes. Unlike articulated robots with rotary joints, Cartesian robots utilize linear actuators for movement, making them well-suited for tasks that require straight-line precision.
- SCARA Robots: Selective Compliance Assembly Robot Arm (SCARA) robots have three rotary joints and one linear joint, providing fast and precise horizontal movements. SCARA robots are ideal for tasks that require speed and accuracy, such as assembly and pick-and-place operations.
Applications of Industrial Robots
From assembly lines to hazardous environment applications of industrial robots are given below.
- Manufacturing and Assembly
- Welding (Arc Welding, Spot Welding)
- Painting and Coating (Spray Painting, Powder Coating)
- Quality Inspection (Vision Systems)
- Material Removal (Grinding and Polishing)
- Machine Tending (Loading and Unloading Machines)
- Pick and Place (Warehousing and Distribution)
- Food Industry (Sorting, Cutting, and Packaging)
- Pharmaceuticals (Packaging and Inspection)
- Medical Applications (Surgical Procedures)
- Construction (Bricklaying, Concrete Spraying, Demolition)
- Agriculture (Planting, Harvesting, Sorting)
- Mining (Exploration, Drilling, Material Handling)
- Textile Industry (Sewing, Cutting, Material Handling)
- Space Exploration (Exploration, Sample Collection, Maintenance)
Supervisory Control and Data Acquisition (SCADA)
Role of SCADA in Industrial Automation:
SCADAs play a pivotal role as important elements of industrial automation in industry by enabling real-time monitoring, data acquisition, remote control, alarm management, historical data logging, and security measures, contributing to enhanced efficiency, reliability, and compliance in industrial processes.
SCADA Components and Architecture:
SCADA systems consist of various components, including sensors, Remote Terminal Units (RTUs), Programmable Logic Controllers (PLCs), Human-Machine Interface (HMI), communication networks, and servers, organized in a hierarchical architecture to enable real-time monitoring, control, and data acquisition in industrial processes.
DCS as elements of industrial automation
Functions of DCS
DCS (Distributed Control System) functions as crutial elements of industrial automation and include real-time process control, monitoring, data acquisition, and communication, providing a centralized platform for seamless coordination and optimization of industrial processes.
Integration with PLCs and SCADA
DCS seamlessly integrates with PLCs (Programmable Logic Controllers) and SCADA (Supervisory Control and Data Acquisition) systems, forming a cohesive network that enhances overall control, monitoring, and automation in industrial processes.
Control Strategies in Industrial Automation
Embark on a journey through the intricate world of Control Strategies in Industrial Automation, unraveling the nuances of open-loop, closed-loop, and model-based control systems.
Open-Loop Control
Open-loop control is a control system where the output is not directly influenced by the system's current state. In this system, the control action is predetermined and not based on feedback about the actual output. It lacks the ability to make real-time adjustments based on the system's performance.
Advantages and Disadvantages
Advantages of Open-Loop Control:
- Simplicity: Open-loop control systems are often simpler in design and implementation, making them cost-effective and easier to operate.
- Stability: They tend to be more stable since there is no reliance on feedback, which eliminates the risk of instability caused by delayed or incorrect feedback information.
- Predictability: The system behavior is predictable and can be precisely determined based on the input and the system model.
Disadvantages of Open-Loop Control:
- Lack of Adaptability: Open-loop systems do not adjust to changes in the environment or disturbances, making them less adaptable to variations or uncertainties.
- Limited Accuracy: The absence of feedback means that open-loop systems may not provide accurate control, as they cannot correct for errors or disturbances.
- Sensitivity to Parameter Variations: Open-loop control can be sensitive to changes in the system's parameters, leading to reduced performance or even system failure.
- Inability to Compensate for Disturbances: External disturbances or variations in the system are not accounted for, which can result in poor performance in the presence of disturbances.
Closed-Loop Control
Closed-loop control, also known as feedback control, is a control system where the output is continuously monitored and compared to the desired reference signal. The system adjusts its input based on the feedback information to minimize the difference between the actual output and the desired output, providing a dynamic and self-regulating mechanism.
Feedback Systems
As elements of industrial automation, Closed-loop control systems utilize feedback to maintain alignment between the actual system output and the desired reference signal. Sensors measure the system's performance, generating an error signal that represents any deviation from the desired state. The controller processes this error signal and adjusts the system's input accordingly. Actuators then implement these adjustments, influencing the system's behavior.
This continuous feedback loop enables real-time monitoring and dynamic adjustments, contributing to stability, accuracy, and adaptability in response to changes or disturbances. Closed-loop systems, by iteratively comparing and correcting, offer improved performance compared to open-loop systems, making them widely used in various applications requiring precise and responsive control.
PID Controllers as elements of industrial automation
PID controllers, or Proportional-Integral-Derivative controllers, are a fundamental component of feedback control systems employed in diverse engineering and industrial applications. Operating by continuously adjusting system inputs, the controller's proportional component addresses current errors, the integral component handles accumulated past errors to eliminate steady-state discrepancies, and the derivative component anticipates future errors by considering the rate of change.
This dynamic combination enables PID controllers to effectively minimize the difference between the desired setpoint and the actual output, providing precise and stable control in processes such as temperature regulation, motor speed control, and various industrial automation systems.
Model-Based Control
Predictive Control
Predictive control, also known as model predictive control (MPC), is an advanced control strategy used in industrial processes and systems. Unlike traditional control methods as elements of industrial automation, predictive control utilizes a dynamic model of the system to predict its future behavior and optimize control inputs accordingly. The controller considers a prediction horizon into the future, systematically calculating the optimal control actions that will minimize a predefined cost function.
This approach allows predictive controllers to anticipate and proactively address constraints, disturbances, and variations in the system. Predictive control is particularly valuable in complex processes where the ability to foresee and adapt to future conditions is crucial for achieving optimal performance and efficiency.
Adaptive Control
Adaptive control is a dynamic control strategy employed in systems where the characteristics or parameters of the controlled process are subject to change over time. This approach allows the controller to adjust its parameters continuously based on real-time observations and feedback, ensuring optimal performance despite uncertainties and variations. Adaptive control systems use adaptive algorithms to identify and track changes in the system's dynamics, enabling the controller to adapt and tune itself accordingly.
This flexibility is particularly valuable in situations where the system's operating conditions or characteristics may evolve, such as in processes with varying loads or environmental conditions. Adaptive control contributes to improved stability, efficiency, and robustness in the face of changing dynamics within the controlled system and play important role as elements of industrial automation.
Future Trends in Industrial Automation
Embark on a journey into the future of industrial automation, exploring the cutting-edge technologies shaping Industry 4.0 and the integration of Artificial Intelligence.
Industry 4.0
Cyber-Physical Systems as elements of industrial automation
Cyber-Physical Systems (CPS) refer to integrated systems where computational algorithms and physical processes are tightly interconnected. These systems merge the cyber world of computing and communication with the physical world, creating a symbiotic relationship. CPS often involve interconnected sensors, actuators, and computing devices that monitor and control physical processes in real time.
This integration enables seamless communication, data exchange, and decision-making, fostering a more efficient and responsive interaction between the digital and physical components. Examples of Cyber-Physical Systems include smart grids, autonomous vehicles, industrial automation, and smart healthcare systems, where the synergy between the cyber and physical components results in enhanced capabilities, real-time adaptability, and improved overall system performance.
Internet of Things (IoT) as elements of industrial automation
Uncover the transformative impact of IoT on industrial automation. Discuss real-world applications, from smart factories to predictive maintenance.
Artificial Intelligence in Automation
Machine Learning (ML) has become a transformative force in industrial automation, offering advanced capabilities for data analysis, pattern recognition, and decision-making. In industrial settings, ML algorithms are applied to process large volumes of data from sensors, machines, and other sources to identify patterns, anomalies, and correlations. Predictive maintenance is a prominent application, where ML models analyze equipment data to predict potential failures, optimizing maintenance schedules and minimizing downtime. ML also enhances production efficiency through predictive analytics, quality control, and process optimization. Adaptive control systems leverage ML to continuously learn and adjust parameters, improving the responsiveness and adaptability of industrial processes.
Overall, the integration of machine learning in industrial automation brings about increased efficiency, reduced costs, and improved overall system performance by harnessing the power of data-driven insights and intelligent decision-making.
Challenges and Considerations
Cybersecurity in Industrial Automation
It involves implementing measures to protect industrial control systems (ICS), data, and networks from cyber threats and unauthorized access. Key aspects of cybersecurity in industrial automation include
- Network Security
- Authentication and Authorization
- Data Encryption
- Patch Management
Watch our Video on "Essential Element of Automation".
Conclusion
In essence, elements of industrial automation are a catalyst for innovation and competitiveness in the manufacturing sector. As industries strive to stay ahead in an ever-evolving market, the adoption of automation technologies emerges not just as a strategic choice but as an imperative for sustained growth and excellence. In the subsequent sections, we will delve deeper into the fundamental components and advanced technologies that constitute the realm of industrial automation.